The condenser, one of the fundamental components of a refrigerating machine, is the main actor of the heat exchange between the refrigerant and the external environment. Through the condenser, the heat absorbed by the machine in order to achieve the cooling effect is discharged outside it. An efficient condenser has a significant impact on the efficiency of the whole machine as well as on its operating temperature range.
In the category of air-cooled refrigeration machines, the most widely used condensers to date are copper tube - aluminium fin coils. In recent years, however, a new technology made its way to the HVACR world: the microchannel condensers.

More than reliable and now almost a standard in the automotive sector, this technology presents substantial differences compared to the conventional copper-aluminum condenser. Firstly, the microchannel battery is made entirely of aluminum. The tubes, flat and wide, are directly welded on the two collectors located on the sides of the coil. The fins, obtained from a single corrugated aluminum sheet, are placed between two consecutive tubes and fixed to them.
A variable number of channels, which can have multiple geometries, insist along the tubes. These channels have extremely small internal sections, especially when compared to the tubes used in copper-aluminum coils.
This feature allows an effective heat exchange between the condensing fluid and the battery channels, making the microchannel condensers generally more performing than the same size copper-aluminum counterpart. In addition to that, the fins are louvered, allowing an optimized heat exchange also between the coil and the air.
The refrigerant is circulated inside the condenser with a variable number of septa placed inside the collectors sectioning the volume and separating appropriate zones. In this way, a specific path for the refrigerant is defined, with it crossing the battery in its length a certain number of times.
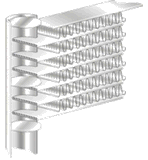
In general, microchannel batteries are not rigidly attached to the machine's structure: they are instead connected through deformable supports that fulfil the dual function of damping machine vibrations (not to transfer them directly to the battery) and offering an additional degree of freedom to the battery allowing its thermal expansion at high temperatures.
With the same dimensions (width, height) and at the same working conditions, a microchannel coil can offer comparable performances as its copper-aluminum counterpart with ¼ of the thickness. This is made possible by to the optimized heat exchange between both the refrigerant and the battery and the battery and the air. The highly reduced thickness of this type of battery also makes it very easy to clean.
It is also possible to apply, as for the traditional finned coils, a protective coating to the microchannel coils, in order to increase their resistance to atmospheric and aggressive agents and therefore increasing their useful life, especially in marine environments or in particularly hostile atmospheres.
Entirely made in aluminum, the microchannel battery weighs just over a third of an equivalent copper-aluminum coil, in which more than half of the total mass is imputable to the copper pipes and collectors. Moreover, thanks to the presence of a single material there will not be galvanic corrosion phenomena.

One of the main advantages of a microchannel battery to the copper-aluminum counterpart is having an extremely low internal volume (up to 80-90% less). This factor brings benefits on several levels: lower volume means less refrigerant inside the condenser, which generally contains a good part of the total refrigerant charge of the machine. As a rule of thumb, a conventional condenser contains from 30% to 50% of the total refrigerant mass of the machine: the use of a microchannel condenser dramatically reduces the total mass of refrigerant needed and, consequently, the relative cost. Furthermore, lower refrigerant charge leads to less restrictive prescriptions within the F-Gas regulation. A low internal volume also allows falling into low PED categories.
Frigosystem offer this type of condenser on medium and high power chillers, both in combination with Scroll compressors in the RACA PLUS ENERGY series, and with screw compressors in the RACA HEAVY DUTY series, in combination with the following refrigerant gases: R410A, R134a, R513A, R1234ze, and R454B.
by Frigosystem Experts